Оценка возможности применения крупногабаритной штамповой оснастки, полученной с помощью аддитивных технологий
Оценка возможности применения крупногабаритной штамповой оснастки, полученной с помощью аддитивных технологий
Аннотация
За последние 7 лет аддитивное производство пережило значительный взлёт, открыв новые горизонты в промышленности и науке благодаря возможности создания деталей сложной геометрической формы. Качество моделей, созданных с помощью 3D-печати, часто сравнимо с традиционными методами производства. Стоит ли утверждать, что за такой инновационной технологией стоит будущее?
Цель данной статьи – оценить возможность применения штамповой оснастки полученной с помощью 3D печати с использованием разработанного технологического процесса изготовления специальной коробчатой тары для хранения и перевозки боеприпасов и капсюлей воспламенителей.
Актуальность темы обусловлена возможностью существенно снизить стоимость разработки и производства прототипов тяжелой штамповой оснастки с помощью аддитивных технологий. Это позволит сократить издержки на проектирование и изготовление, а также ускорить весь производственный цикл получения детали.
Работа также будет являться актуальной за счет того, что в современном машиностроении значительную роль играет технологическая конкуренция, а оперативное создание и оценка прототипов новой продукции, с использованием современных технологий, позволит компаниям-производителям значительно превосходить своих конкурентов путем снижения времени, а также материальных затрат и ресурсов на их производство.
1. Введение
В момент решения задачи проектирования изделий массового или единичного производства разработчик сталкивается с проблемой – необходимостью визуализации внешнего вида, рационализации выполнения конфигураций, возможностью собираемости с комплектующими деталями. Ещё одной из ключевых проблем, стоящей перед современной машиностроительной отраслью промышленности, является создание конкурентоспособных изделий в заданные сроки, с требуемым качеством и при минимальных расходах .
Решением данных проблем является наличие физического прототипа – образца изготавливаемой детали, максимально (насколько позволяет оборудование) приближенной к своей компьютерной разработке – 3D модели , .
Прототипирование – технологическая операция создания опытных образцов или рабочих моделей систем для демонстрации заказчику или проверки возможности исполнения и реализации .
Процесс используется в машиностроении, приборостроении и других технических областях. Прототипирование объектов с помощью формирования их компьютерных моделей взяло своё начало примерно в 80-е года . Ранее прототипы объектов создавали другими способами – либо операциями изменения формы заготовки (прессование, штампование), либо путем снятия стружки с заготовки (фрезерование, точение). Таким образом, прототипирование позволяет наиболее ярко отразить внутреннее и наружное устройство системы готового продукта и значительно увеличить адаптивность производства .
Когда речь идет о прототипировании, нужно проверить несколько вещей:
1. Функциональность: убедиться, что прототип выполняет основные функции и задачи, которые он должен решать. Проверить, что все элементы работают должным образом и что прототип оснастки взаимодействует с пользователем так, как задумано .
2. Внешний вид: оценить внешний вид прототипа с точки зрения дизайна и технологичности. Убедиться, что конфигурация соответствует компьютерной разработке, а также обеспечивает удобство использования.
3. Техническая проверка: проверить техническую выполнимость прототипа. Убедиться, что используемые технологии и инструменты подходят для реализации задуманного функционала .
4. Задачи и сценарии использования: протестировать прототип на выполнение различных задач и сценариев использования. Убедиться, что он эффективно решает эти задачи и предоставляет пользователю все необходимые функции .
5. Важно помнить, что проверка прототипа – это итеративный процесс, и результаты проверки могут привести к дальнейшей модификации и улучшению прототипа.
Преимущества технологий прототипирования:
1) сокращение длительности технической подготовки производства новой вводимой продукции в 2-4 раза;
2) снижение себестоимости продукции, особенно в мелкосерийном или единичном производстве в 2-3 раза;
3) значительное повышение адаптивности производства;
4) повышение конкурентоспособности производства;
5) сквозное использование компьютерных технологий, интеграция с системами САПР.
2. Материалы и методы
В статье описан новый альтернативный способ и проведена его опытно технологическая апробация с использованием оснастки, полученной с использованием аддитивных технологий.
Способ относится к листовой штамповке и может быть использован в прессовых производствах для штамповки коробчатых деталей разнообразной в сечении конфигурации из листовых материалов, металлов и неметаллов, преимущественно для штамповки-вытяжки коробчатых деталей транспортных средств, бытовой и другой техники на прессах простого действия или многопозиционных прессах – автоматах , .
Задачами этого способа являются: повышение качества коробчатой детали получаемой вытяжкой правкой и калибровкой, уменьшение количества операций, повышение технологичности, повышение качества изделий, уменьшение себестоимости одной детали.
Задачи решаются за счёт того, что предварительно определяют предельную глубину, угол наклона стенки первого полуфабриката из условия, чтобы на всех этапах вытяжки максимальное растягивающее напряжение в опасной точке стенки вытягиваемого полуфабриката постепенно увеличивалось и на конечном этапе вытяжке стало равным пределу текучести металла. На первой операции выполняют вытяжку полуфабриката с донной частью, по конфигурации и размерам сразу же соответствующей донной части коробчатой детали. На последующих операциях образуются наклонные стенки на предельную (без разрушения) глубину, первый угол наклона уменьшают, глубину вытяжки увеличивают, при этом посредством подушки пресса или буфера штампа. На прижиме штампа, прижимающего край полуфабриката, создают силу, заталкивающую в процессе вытяжки наклонную стенку полуфабриката в матрицу штампа и облегчающую процесс вытяжки без разрушения полуфабриката. На последней операции вытяжки получают полуфабрикат с формой и размерами, соответствующими форме и размерам коробчатой детали с учетом припуска на обрезку неровного края полуфабриката, и одновременно с вытяжкой выполняют также правку складок, допустимых на предыдущих этапах вытяжки, по всей поверхности заготовки .
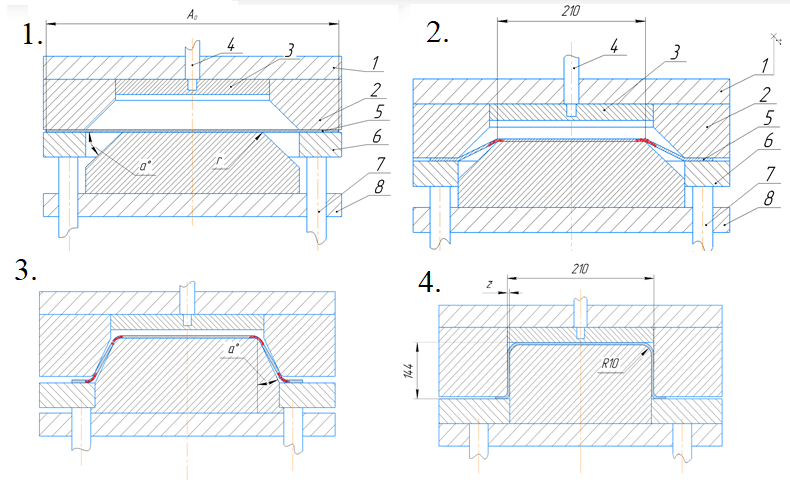
Рисунок 1 - Предлагаемый процесс изготовления детали: 1 – начало процесса, 4 – завершение процесса
Примечание: расшифровка обозначений: 1 – плита верхняя; 2 – матрица вытяжки; 3 – выталкиватель; 4 – направляющая выталкивателя; 5 – заготовка; 6 – прижим; 7 – штифт гидроподушки пресса; 8 – плита нижняя
Для анализа вытяжки листового металла используются шелл-элементы (SHELL181 в ANSYS), которые позволяют учитывать толщину детали. В некоторых случаях, для высокой точности моделирования тонких участков, могут использоваться солид-элементы (SOLID185, например).
Выбор размера сетки – это компромисс между точностью и вычислительными затратами. В зонах с высокими градиентами напряжений (например, в углах детали, зонах перегибов) сетка должна быть более мелкой. Для большей эффективности можно использовать адаптивную сетку, которая автоматически измельчается в критических областях. В расчетах была использована мелкая сетка – от 36° до 12°. Tetrahedrons – метод задания сетки позволяет генерировать объемные сетки с элементами, имеющими форму тетраэдров, на основе одного из двух методов: Patch Conforming и Patch Independent (раздел Algorithm метода Tetrahedrons). Метод является предпочтительным в том случае, если исходная геометрия содержит изгибы, скругления, при этом имеет высокое качество т.е. в ней отсутствуют проблемные зоны являющиеся следствием некорректного построения в CAD.
Начальные и граничные условия при моделировании процесса вытяжки деталей в ANSYS критически важны для получения достоверных результатов.
Начальные условия:
1. Геометрия: начальное состояние моделируется исходной геометрией детали до начала процесса вытяжки. Важно убедиться в отсутствии ошибок в геометрии, таких как самопересечения или несоответствия. Деталь импортирована в ANSYS в формате STEP214.
2. Напряжения и деформации: в большинстве случаев начальное состояние предполагает отсутствие напряжений и деформаций в детали. Это стандартное начальное условие для статических расчетов.
Граничные условия определяют взаимодействие модели с окружающей средой и задают внешние воздействия на деталь во время процесса вытяжки. Они включают в себя:
1. Защемление (фиксированные перемещения): определяет участки детали, которые жестко зафиксированы и не могут перемещаться. Это обычно область, удерживающая заготовку в штампе. В ANSYS это задаётся через меню Constraints.
2. Перемещения (Prescribed displacement) – это наиболее распространенный подход для моделирования вытяжки. Перемещения задаются на пуансоне, определяя его движение в процессе вытяжки. В ANSYS это осуществляется через Displacement в меню Loads.
3. Контактные взаимодействия: необходимо точно определить контактные поверхности между:
4. Деталью и пуансоном: определяет передачу сил от пуансона к детали.
5. Деталью и матрицей: определяет взаимодействие детали с матрицей, ограничивая ее деформацию.
6. Деталью и прижимом: определяет фиксацию детали в штампе.
Для каждой контактной пары нужно задать параметры контакта в ANSYS, включая:
– тип контакта: (например, поверхностный контакт, точечный контакт);
– коэффициент трения: влияет на распределение сил и деформаций;
– допуск: учитывает небольшие зазоры между поверхностями.
Была смоделирована оснастка в программе Компас 3D, а так же выполнены расчеты процесса вытяжки в программе ANSYS и QForm, представленные на рисунке 2, 3.
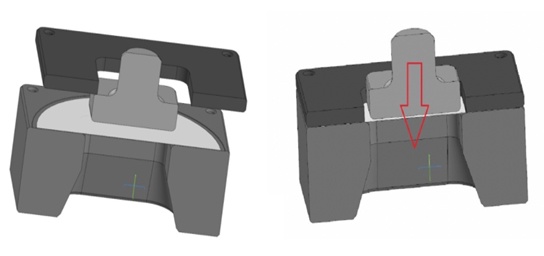
Рисунок 2 - Схема, используемая в расчете
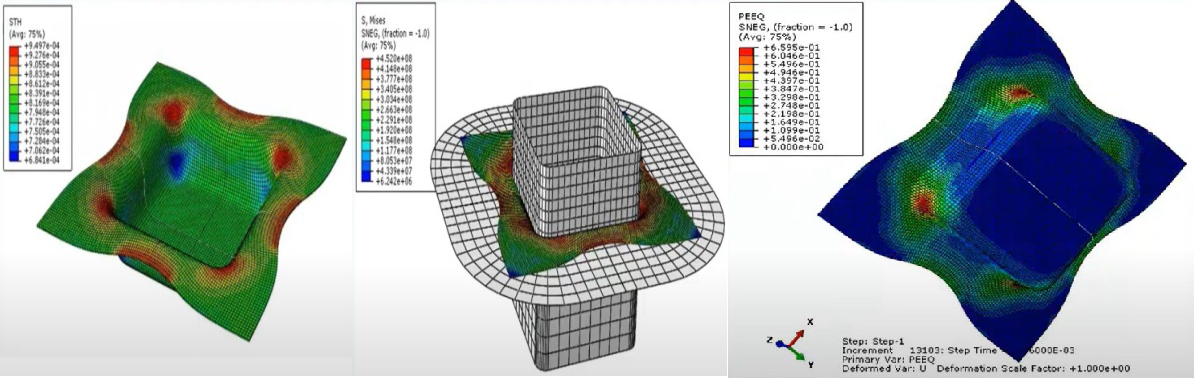
Рисунок 3 - Результаты расчета вытяжки детали коробчатой формы
Матрица и пуансон из пластика используются в штамповке, где требуется создание небольших или средних объемов продукции с использованием пластиковых материалов. Матрица и пуансон – это две части пресс-формы, используемой в процессе штамповки.
Матрица – это нижняя половина пресс-формы, которая фиксируется на плиту пресса. Она имеет отверстия, в которые проникает пластиковый материал при прессовании.
Пуансон – это верхняя половина пресс-формы, которая также имеет отверстия, соответствующие отверстиям матрицы. Пуансон фиксируется на ползуне пресса (реже на столе) и перемещается вниз для давления на пластиковый материал, что позволяет ему принимать форму матрицы. Пластиковые материалы обычно используются в производстве деталей небольшого и среднего размера, таких как крышки, крышки для бутылок, корпуса электронных устройств, пластиковые элементы автомобильных деталей и многие другие изделия.
Преимуществом использования матрицы и пуансона из пластика является их легкий вес, что упрощает их переноску и установку на пресс. Кроме того, пластиковые матрицы и пуансоны не коррозируют и не подвержены износу, как металлические матрицы и пуансоны, что увеличивает их долговечность и снижает затраты на их замену. Однако они не могут выдерживать высокие температуры и высокие уровни давления, что ограничивает их применение в тяжелых условиях производства.
Производство матрицы из пластика имеет свои плюсы и минусы.
Плюсы:
1) низкая стоимость: пластиковые матрицы обычно стоят значительно дешевле, чем металлические аналоги. Это может снизить затраты на производство и замену матрицы;
2) легкий вес: пластиковые матрицы значительно легче металлических, что облегчает их транспортировку, установку и обслуживание;
3) простота изготовления: пластиковые матрицы могут быть легко изготовлены с использованием технологий 3D-печати или методов литья под давлением. Это позволяет быстро создавать новые матрицы или модифицировать существующие;
4) коррозионная стойкость: пластиковые матрицы не подвержены коррозии, что позволяет им дольше сохранять свою форму и функциональность в сравнении с металлическими матрицами.
Минусы:
1) ограничения по температуре и давлению: пластиковые матрицы не могут выдерживать высокие температуры и высокие уровни давления, что ограничивает их применение в некоторых процессах штамповки или литья;
2) ограниченная прочность: пластиковые матрицы обычно имеют более низкую прочность и износостойкость по сравнению с металлическими матрицами. Они могут стереться или повреждаться при использовании с абразивными материалами или в условиях высокой нагрузки;
3) ограничения по размеру и сложности формы: пластиковые матрицы могут быть ограничены в размере и сложности формы из-за свойств пластиковых материалов и методов их изготовления. Это может ограничить их применение в некоторых проектах;
4) ограничения по материалам: некоторые материалы, такие как некоторые металлы или сплавы, не могут быть штампованы с использованием пластиковых матриц из пластика.
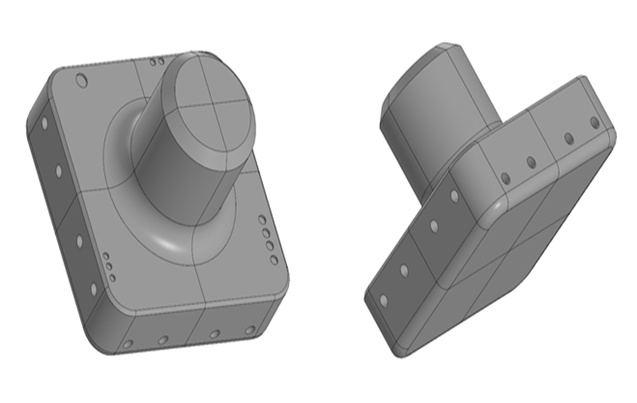
Рисунок 4 - 3D модель пуансона
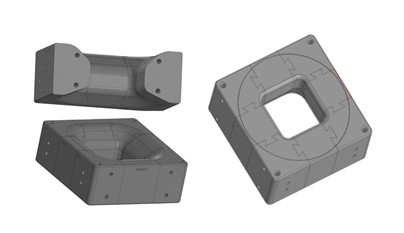
Рисунок 5 - 3D Модель матрицы вытяжки
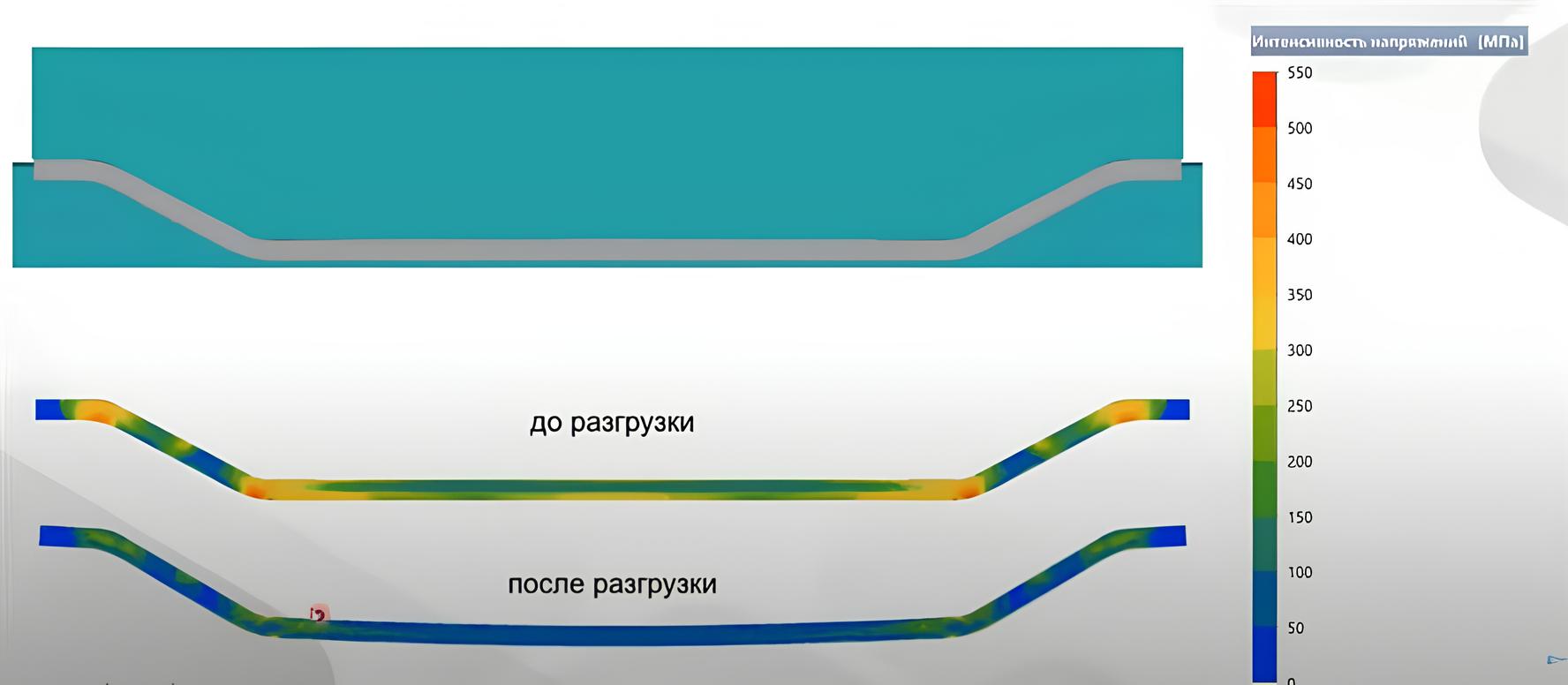
Рисунок 6 - Наглядное изображение прогиба дна заготовки, полученное в программе QForm
Таблица 1 - Характеристики пластика PETG
Характеристики | Метод испытаний | Единица измерения | Значение |
Плотность | ISO 1183 | кг/м³ | 1270 |
Модуль упругости при изгибе | ISO 178 | МПа | 2100 |
Предел текучести при растяжении | ISO 527 | МПа | 50 |
Относительное удлинение при разрыве | ISO 527 | % | 40 |
Ударная вязкость по Шарпи (23°C) | 179/1ep | кДж/м² | н/р |
Ударная вязкость по Шарпи образца с надрезом (23°C) | 179/1epA | кДж/м² | 8 |
Ударная вязкость по Шарпи образца с надрезом (-40°C) | 179/1epA | кДж/м² | 2 |
Твердость по Шору, метод D | ISO 868 | - | 117 |
Температура размягчения по Вика 10Н/120°C | 306/A120 | °C | 82 |
Температура размягчения по Вика 50Н/120°C | 306/B120 | °C | 78 |
Все части матрицы были напечатаны, зачищены и обезжирены. Далее была проведена сборка и склейка частей матрицы и пуансона. На рисунке 7 представлено фото матрицы, которая стянута шпильками и фото пуансона перед сборкой.
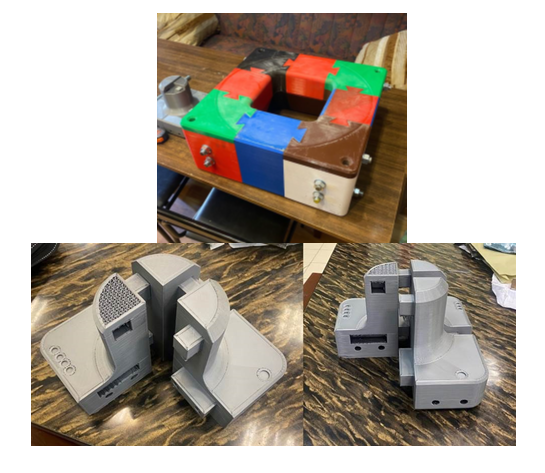
Рисунок 7 - Фото матрицы и пуансона
3. Трение при операциях
Трение между пластиком (оснасткой) и металлом (заготовкой) может возникать при штамповке, если металлическая деталь проходит через матрицу и пуансон, которые изготовлены из пластика. Трение может вызвать повреждение поверхности детали, увеличение износа матрицы и пуансона, а также привести к потере точности формы изготавливаемой детали , . Одним из способов уменьшения трения при штамповке пластиковых деталей является смазывание матрицы и пуансона. Для этого можно использовать специальные масла или смазки, которые помогают снизить трение и повысить точность формы изготавливаемой детали.
Еще одним способом является использование специальных пластмассовых материалов, которые имеют более низкий коэффициент трения при контакте с металлом. Это позволяет уменьшить износ матрицы и пуансона, а также повысить точность формы штампуемой детали .
Коэффициент трения между металлом и пластиком может варьировать в зависимости от конкретных материалов, их состояния поверхности, окружающей среды и других факторов. Несколько примеров коэффициентов трения между различными металлическими и пластиковыми материалами приведены в таблице 2 .
Таблица 2 - Коэффициенты трения между металлическими и пластиковыми материалами
Материалы, подвергаемые трению | Коэффициент трений скольжения |
Коэффициент трения между металлом (например, сталью) и LDPE | 0,2-0,3 |
Коэффициент трения между металлом и PP | 0,2-0,4 |
Коэффициент трения между металлом и ABS | 0,4-0,6 |
Коэффициент трения между металлом и PC | 0,3-0,6 |
Коэффициент трения между металлом и PA | 0,1-0,6 |
Важно отметить, что указанные значения коэффициента трения являются приблизительными и могут отличаться в зависимости от условий эксплуатации и конкретных свойств материалов. При проектировании и анализе систем, в которых важно учитывать трение между металлом и пластиком, рекомендуется проводить более точные исследования и испытания для определения коэффициентов трения с учетом специфических условий .
4. Проведение эксперимента
Экспериментальное исследование базируется на эмпирических данных, рассчитанных с помощью программ QForm и ANSYS.
Эксперимент и исследование вытяжки коробчатой детали проводился в лаборатории БГТУ «ВОЕНМЕХ» кафедры Е4 на испытательной машине SHIMADZU, а так же на гидравлическом прессе ПО-54.
Технические характеристики испытательной машины SHINADZU AG 100kNx:
– диапазон измеряемых нагрузок 0,1 – 100 кН.;
– тип силоизмерительного датчика – тензорезисторный;
– пределы допускаемой погрешности машины при измерении нагрузки в диапазоне нагрузок от 0,1 до 100 кН – не более 1% от измеряемой величины;
– максимальный ход подвижной траверсы (без силоизмерительных датчиков, захватов и приспособлений) – 1200 мм;
– скорость перемещения активного захвата: от 0,0005 до 1000 мм/мин.;
– пределы допускаемой погрешности поддержания скорости – не более 0,1% в интервале скоростей от 0,5 до 500 мм/мин;
– циклические испытания, не более 3-х циклов в минуту, количество циклов, до 1000 циклов;
– система высокотемпературных испытаний в интервале 300 -1100°С;
– универсальный электронный динамометр для измерения статической силы сжатия. Позволяет в широком интервале нагрузок и скоростей с высокой точностью и чувствительностью проводить механические испытания материалов: металлов, сплавов, композиционных материалов, пластмасс, резин и др. при комнатных и повышенных температурах, что необходимо при разработке новых конструкционных материалов, усовершенствовать режимы термообработки и обработки давлением существующих материалов.
Для проведения эксперимента предварительно были вырезаны заготовки – кружки большого и малого диаметра, квадратные малые – нужны для понимания устройства отцентровки пуансона относительно матрицы. Фото представлены на рисунке 8. На заготовках была предварительно нанесена разметка для более точной центровки пуансона относительно матрицы.
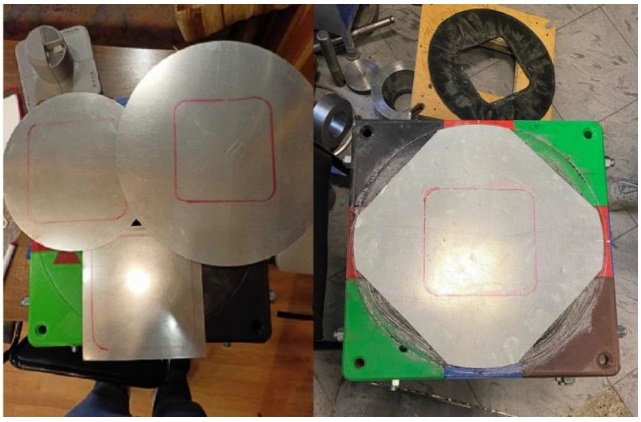
Рисунок 8 - Фото используемых заготовок
1. Температура проведения испытаний – 28 °С
Для вытяжки детали с использованием пластиковой оснастки температура должна быть тщательно подобрана, чтобы избежать деформации или разрушения оснастки. Пластики имеют сравнительно низкую температуру плавления или размягчения. Поэтому, температура процесса должна быть значительно ниже температуры размягчения используемого пластика (PETG).
Помимо температуры размягчения, следует также учитывать:
– продолжительность процесса: даже при температурах ниже температуры размягчения, длительное воздействие тепла может привести к деформации пластика;
– напряжения в оснастке: процесс вытяжки создает напряжения в оснастке. Повышение температуры может усугубить эти напряжения, повышая риск деформации или разрушения .
В большинстве случаев для вытяжки с пластиковой оснасткой оптимальной будет комнатная температура или незначительное повышение температуры (не более 40°C).
Однако, для конкретного случая необходимы эксперименты с различными температурами и мониторингом состояния пластиковой оснастки. В случае сомнений, лучше начать с более низких температур и постепенно повышать их, наблюдая за состоянием оснастки.
2. Скорость нагружения 10 мм/мин
Для вытяжки коробчатой детали часто выбирают умеренную скорость нагружения от 6 мм/мин. Слишком низкая скорость может привести к излишней пластической деформации и утонению стенок, а слишком высокая – к образованию трещин и браку. Оптимальная скорость определяется экспериментально, с учетом свойств материала, геометрии детали и требований к качеству готового изделия. Иногда проводят пробные вытяжки при разных скоростях, чтобы определить оптимальный режим. В данном эксперименте оптимальная скорость нагружения определялась методом последовательных приближений (итераций) .
Первые эксперименты вытяжки были проведены на испытательной машине SHIMADZU для определения силы, необходимой для вытяжки. Фото вытяжки коробки из кружка малого диаметра представлено на рисунке 9.
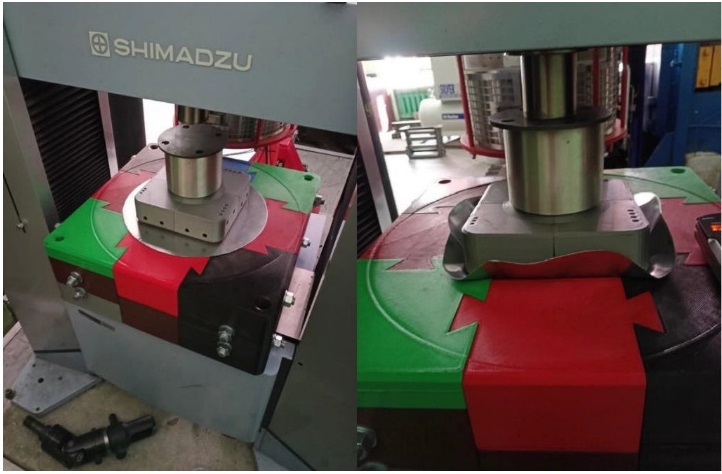
Рисунок 9 - Проведение эксперимента на испытательной машине SHIMADZU
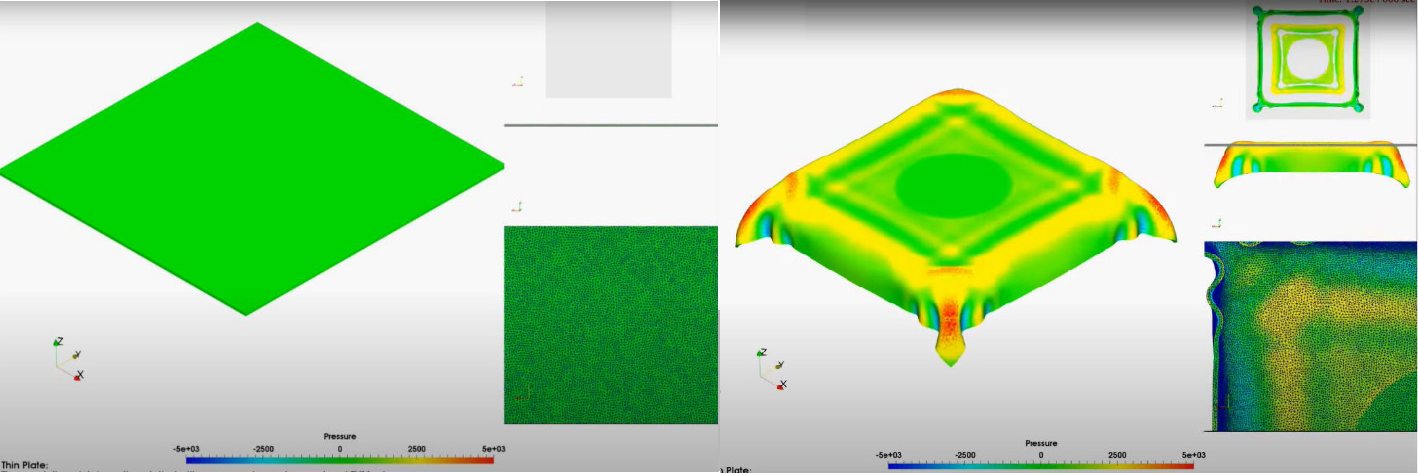
Рисунок 10 - Результаты расчетов
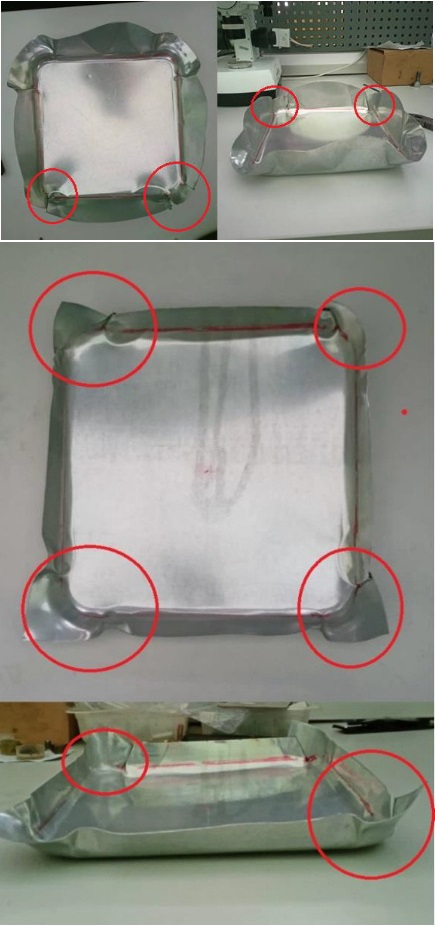
Рисунок 11 - Полученная деталь в результате первого эксперимента на испытательной машине SHIMADZU
Можно заметить, насколько близки полученные расчетные значения и значения, полученные в ходе проведенного эксперимента.
5. Эксперимент на гидравлическом прессе ПО54
Продолжить процесс исследования и получение экспериментальных образцов заготовки позволил гидравлический пресс ПО54, некоторые характеристики которого представлены в таблице 3.
Таблица 3 - Характеристики пресса ПО54
Модель | ПО54 |
Заводской № | 29 |
Год выпуска | 1962 |
Усилие пресса, т | 2000 |
Ход плунжера, мм | 500 |
Давление масла при чеканке, кг/см2 | 400 |
Давление масла при холостом ходе, кг/см3 | 25 |
Вес пресса, т | 20 |

Рисунок 12 - Фото вытяжки при неподвижном пуансоне
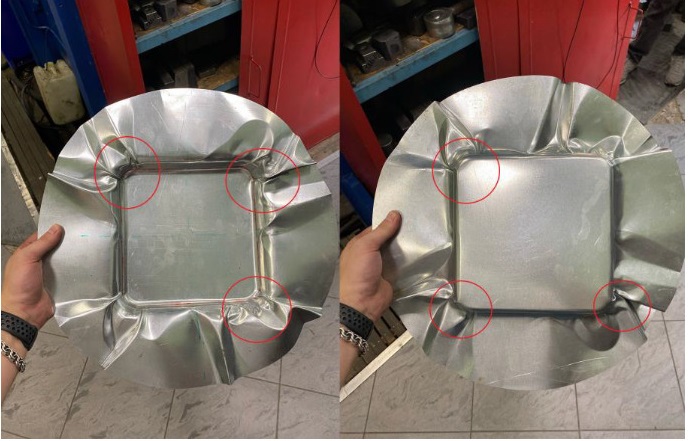
Рисунок 13 - Фото полученной заготовки в процессе вытяжки на прессе ПО54
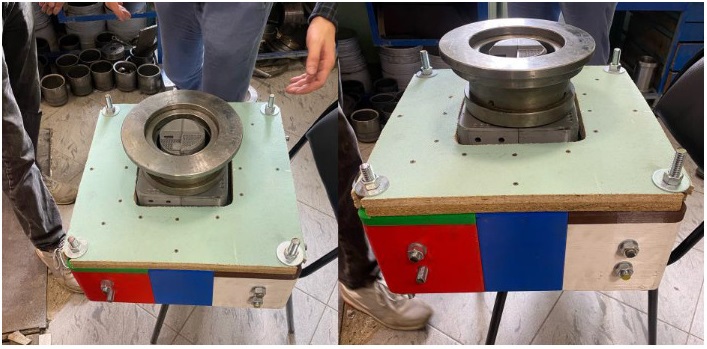
Рисунок 14 - Фото оснастки в сборе
Фото резиновой прокладки представлено на рисунке 15.
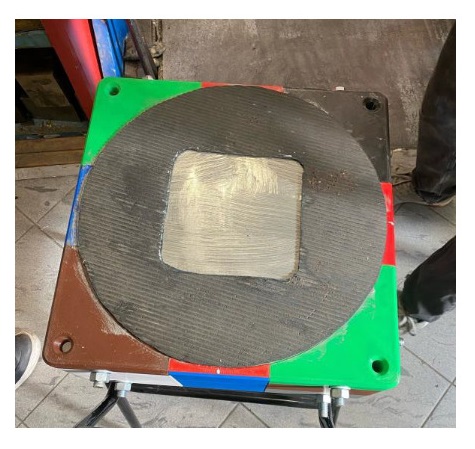
Рисунок 15 - Фото резиновой прокладки
Штамп в сборе представлен на рисунке 16. Результаты эксперимента приведены на рисунке 17.
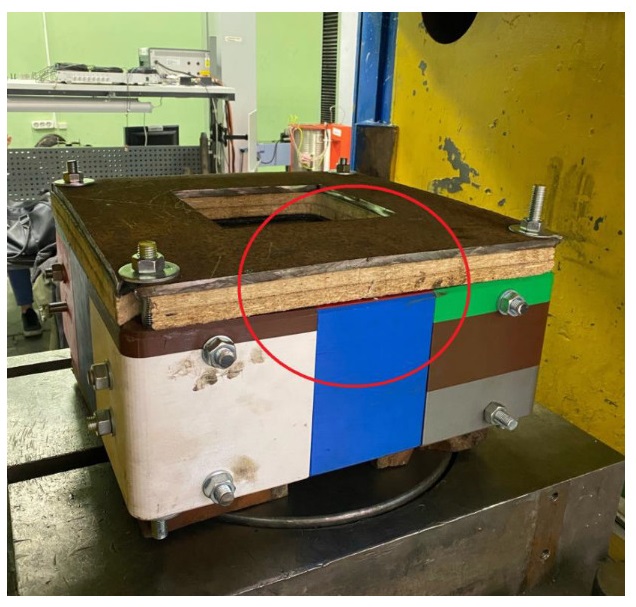
Рисунок 16 - Сборка с металлическим прижимом 12 мм
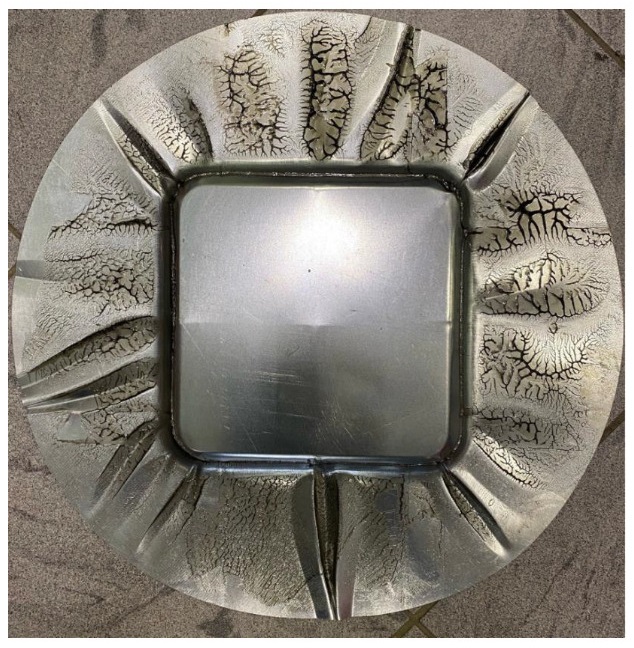
Рисунок 17 - Результат вытяжки с прижимом
6. Результаты и их обсуждение
По результатам эксперимента, вытяжка с прижимом позволяет вытянуть заготовку на глубину до 25 мм с минимальным количеством складок. Возникающие складки являются следствием неплотного прилегания прижима к матрице, матрица, в свою очередь, не является абсолютно жесткой, что, в свою очередь, вызывает «врезание» металла в неё. Таким образом, можно сделать вывод, что при изготовлении оснастки из металла и обеспечением необходимой силой прижима вытяжку коробки, возможно, произвести на высоту до 40 мм без образования складок и разрушения.
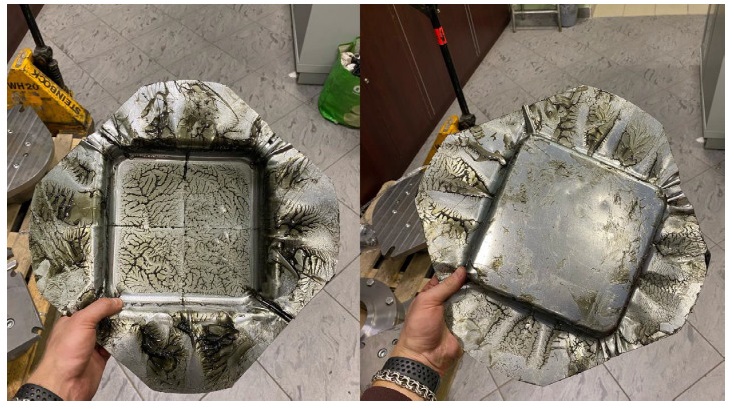
Рисунок 18 - Фото вытянутой коробки из заготовки с обрезными краями
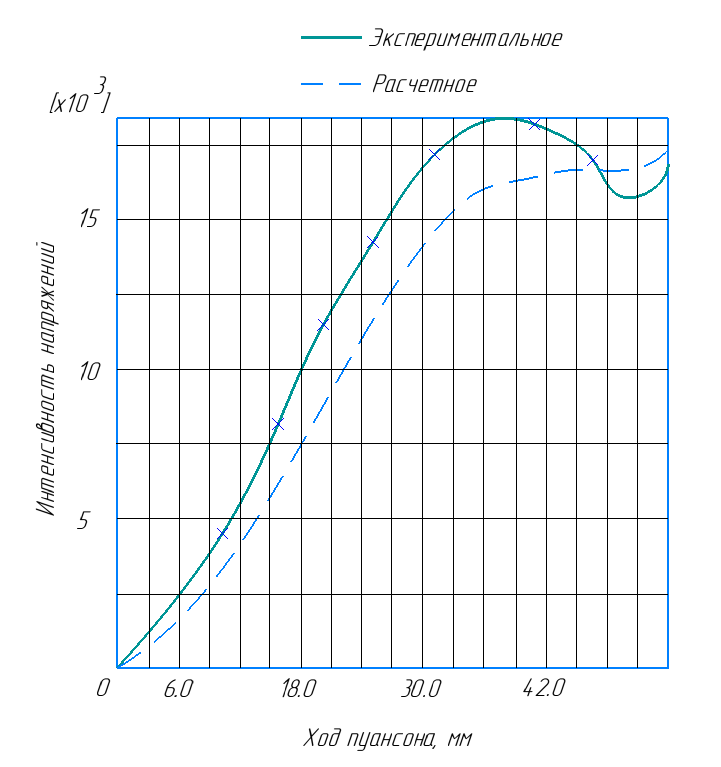
Рисунок 19 - График зависимости. Ход – интенсивность напряжений
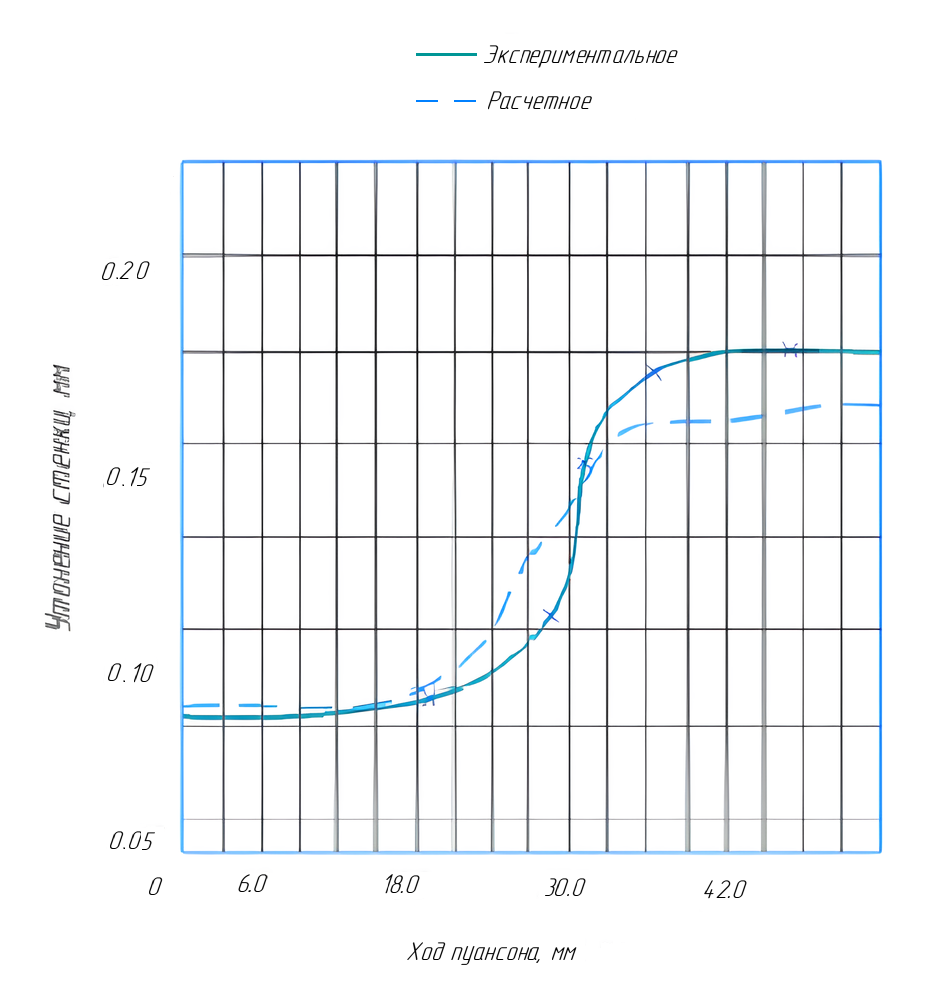
Рисунок 20 - График зависимости. Ход пуансона – утонение стенки
1. Пластиковая матрица подходит лишь для неглубокой вытяжки, вытяжка на высоту более 40мм вызывает складкообразование из-за того, что металл тверже пластика. Металл начинает врезаться в матрицу, вызывая её разрушение.
2. При использовании оснастки из пластика не удастся в полной мере создать усилие прижима с помощью шпилек и гаек. Это в свою очередь вызывает неплотное и неполное прилегание заготовки. При вытяжке происходит «выгибание» прижима, появляются полости, и заготовка из листа металла получает дополнительный зазор, в котором будут образовываться складки.
3. Оснастка из пластика дает возможность в полной мере выявить недостатки проектирования. Матрица и пуансон дешевле в изготовлении, а также скорость их изготовления существенно меньше, нежели подобных аналогов из металла. Минусы – низкая твердость пластика. Данный минус не позволит в полной мере осуществить вытяжку, как было сказано выше.
7. Заключение
В ходе работы был выполнен обзор существующих технологий изготовления корпуса тары для хранения и перевозки боеприпасов и взрывателей. С помощью компьютерного моделирования исследовано влияние однородности поля деформации металла на операциях вытяжки, была смоделирована и напечатана на 3Д принтере оснастка, позволяющая провести эксперимент на гидравлическом оборудовании, который в свою очередь позволил сравнить значения, полученные при моделировании вытяжек.
Технологии создания прототипов с использованием аддитивных методов определяют положение экономики страны в мире, ее стратегические позиции. Наличие технологий дает в руки ученому или конструктору мощные инструменты для реализации новых идей. Технологии позволяют применять новые высокоэффективные материалы, новые методы управления и таким образом обуславливают новое функциональное и интеллектуальное содержание продукта. Отсутствие технологий ограничивает творческий потенциал ученых и конструкторов, вынуждает их применять те технические решения, которые есть в их распоряжении, а не те, которые требуются для достижения целей. Поэтому сами аддитивные технологии являются главным объектом инновационной деятельности.