Многофункциональное оборудование для реализации аддитивно-субтрактивных технологий
Многофункциональное оборудование для реализации аддитивно-субтрактивных технологий
Аннотация
В машиностроении одними из наиболее перспективных являются аддитивные технологии (АТ) выращивания изделий из металлов и сплавов. Они находят все более широкое применение в производстве изделий в различных отраслях машиностроения. Термин «выращивание» связан с постепенным послойным характером изготовления сложного изделия на основе его компьютерной 3D-модели. Проволочные АТ экономически более выгодные в связи с более высокой производительности процесса и, на порядок более низкой стоимости проволоки по сравнению с порошками для популярных технологий SLM и LMD. Кроме того, современной промышленностью освоен выпуск проволоки из широкой номенклатуры материалов, среди которых: алюминий, низколегированные стали, нержавеющие стали, титановые, никелевые сплавы. Недостатком проволочных АТ является более грубая поверхность выращенных изделий. В статье приведены результаты проектирования и применения многофункционального оборудования для совместного использования аддитивных и субтрактивных технологий.
1. Введение
Одним из наиболее перспективных направлений развития аддитивных методов является комплексное использование методов 3D-печати и субтрактивных технологий на одном оборудовании. Примером успешного сочетания этих двух технологий является осаждение/наплавка проволоки методами электродуговой сварки, например Gas Metal Arc Welding (GMA), Wire Arc Additive Manufacturing (WAAM)
, , в сочетании с механической обработкой резанием . Обе технологии в составе спроектированного оборудования являются полностью автоматизированными процессами, использующим массивы CAD/CAM-данных. Причем в процессе наплавки сложноконтурного изделия на основе 3D-модели, можно использовать обычную стандартную (коммерческую) сварочную проволоку, которая выпускается различными производителями (в том числе отечественными) в широкой номенклатуре.Оборудование для WAAM-технологии, как правило, представляет собой аналог 3D-принтера для печати из пластиковых нитей – Fused Deposition Modeling (FDM), но имеет несколько иной принцип плавления материала. Плавление материала проволоки происходит внутри электрической дуги в среде инертного газа. Основными недостатками WAAM-технологии является относительно высокая стоимость оборудования и недостаточная точность размеров полученной заготовки, что вызывает необходимость дополнительной обработки резанием практически всех поверхностей на металлорежущих станках. Как результат, усложнение аппаратурно-технологической схемы, трудоемкости и стоимости изделия
, .Аддитивно-субтрактивная технология подразумевает 3D- печать заготовки и последующую механическую её обработку для устранения погрешности формы, удаления дефектного слоя, повышения точности и уменьшения шероховатости поверхностей детали, к которым предъявляются повышенные требования. В настоящее время этот вид получения деталей все чаще используется для изготовления деталей в единичном производстве макетов и прототипов для изучения особенностей конструкции, еe улучшения и последующего изготовления этих деталей методами механической обработки, например фрезерованием концевыми фрезами. При этом происходит изменение величины сил из-за изменения толщины среза и угол контакта зубьев фрезы. Эти изменения составляющих сил приводят к изменению упругой деформации системы станок – приспособление – инструмент – деталь (СПИД), появлению вибрации, особенно при резонансе, когда частота внешней нагрузки совпадает с частотой собственных колебаний, ухудшению качества обработки и уменьшению надежности работы фрез .
2. Основные результаты
Для реализации совместного использования аддитивных и субтрактивных технологий предлагается оригинальное многофункциональное оборудование с ЧПУ, созданное по модульному принципу. На одной базе портального типа (рисунок 1, а) можно оперативно производить смену инструментальных модулей различного назначения: для наплавки (рисунок 1, в), для обработки резанием (рисунок 1, б). В конструкции установочной плиты предусмотрены технологические отверстия для точной ориентации различных инструментальных модулей относительно оси, достаточное и необходимое количество отверстий, предназначенных для монтажа и надежного закрепления инструментальных модулей. Перемещение рабочих органов по трем осям производится по направляющим и с помощью поворотных головок для наплавки и фрезерования по управляющей программе в соответствии с 3D-моделью детали.
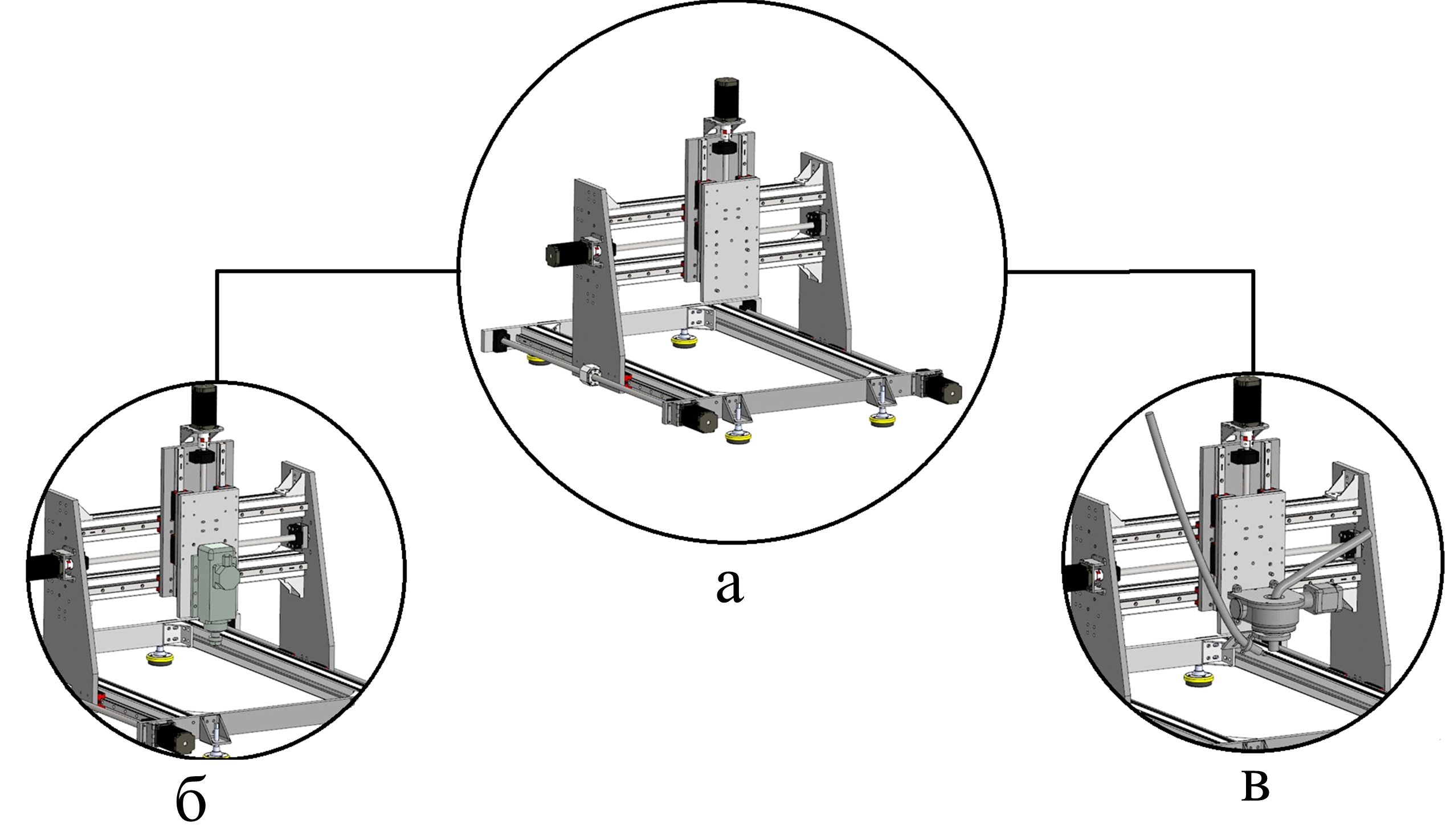
Рисунок 1 - Многофункциональное устройство с ЧПУ:
а - база портального типа; б - модуль для обработки резанием; в - модуль для обработки резанием
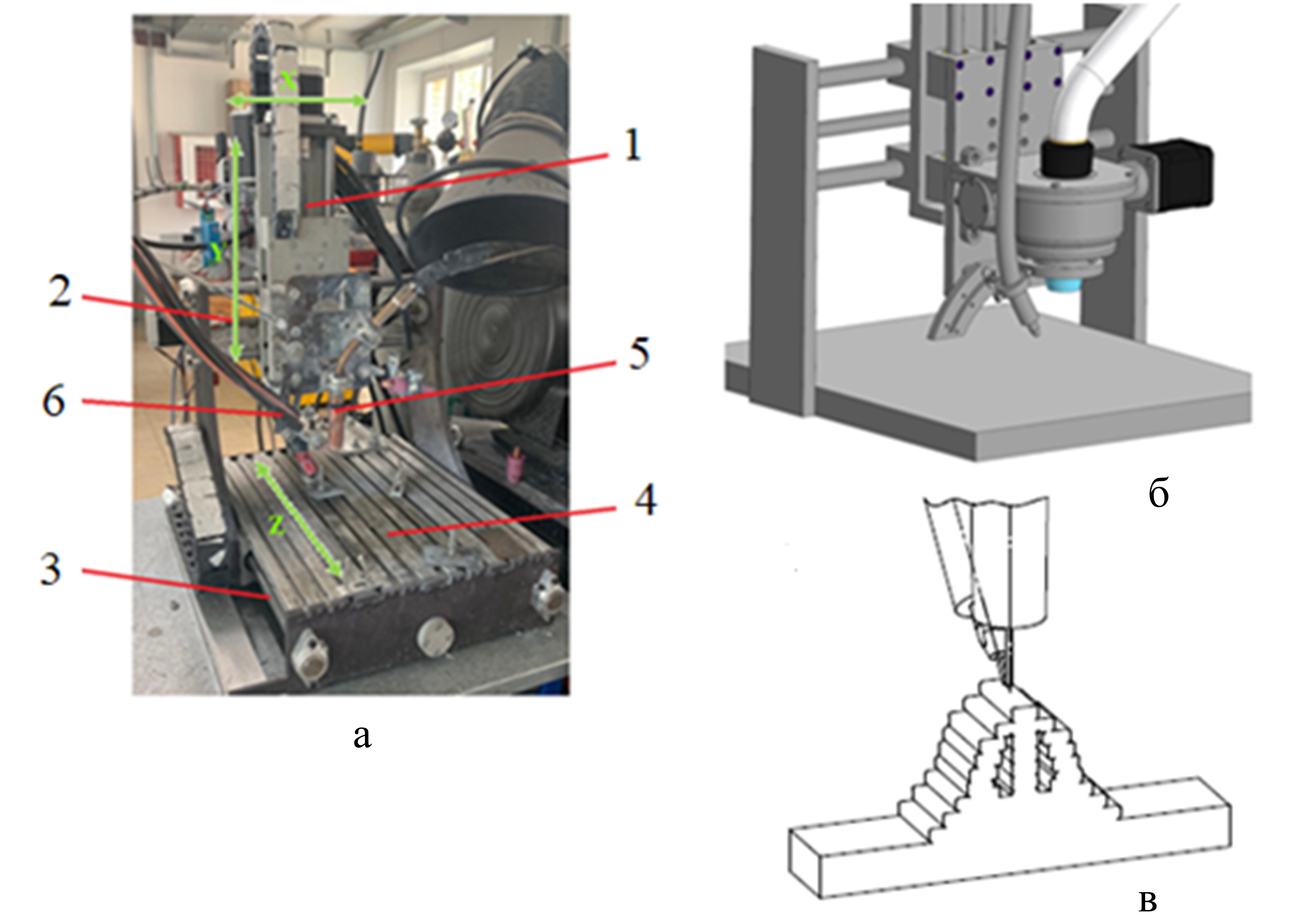
Рисунок 2 - Оборудование для WAAM:
а - установка для дуговой наплавки; б - установка с конструкцией поворотного механизма; в - схема процесса наплавки; 1 - направляющая по оси Z; 2 - направляющая по оси X; 3 - направляющая по оси Y; 4 - стол; 5 - основная горелка; 6 - дополнительное сопло
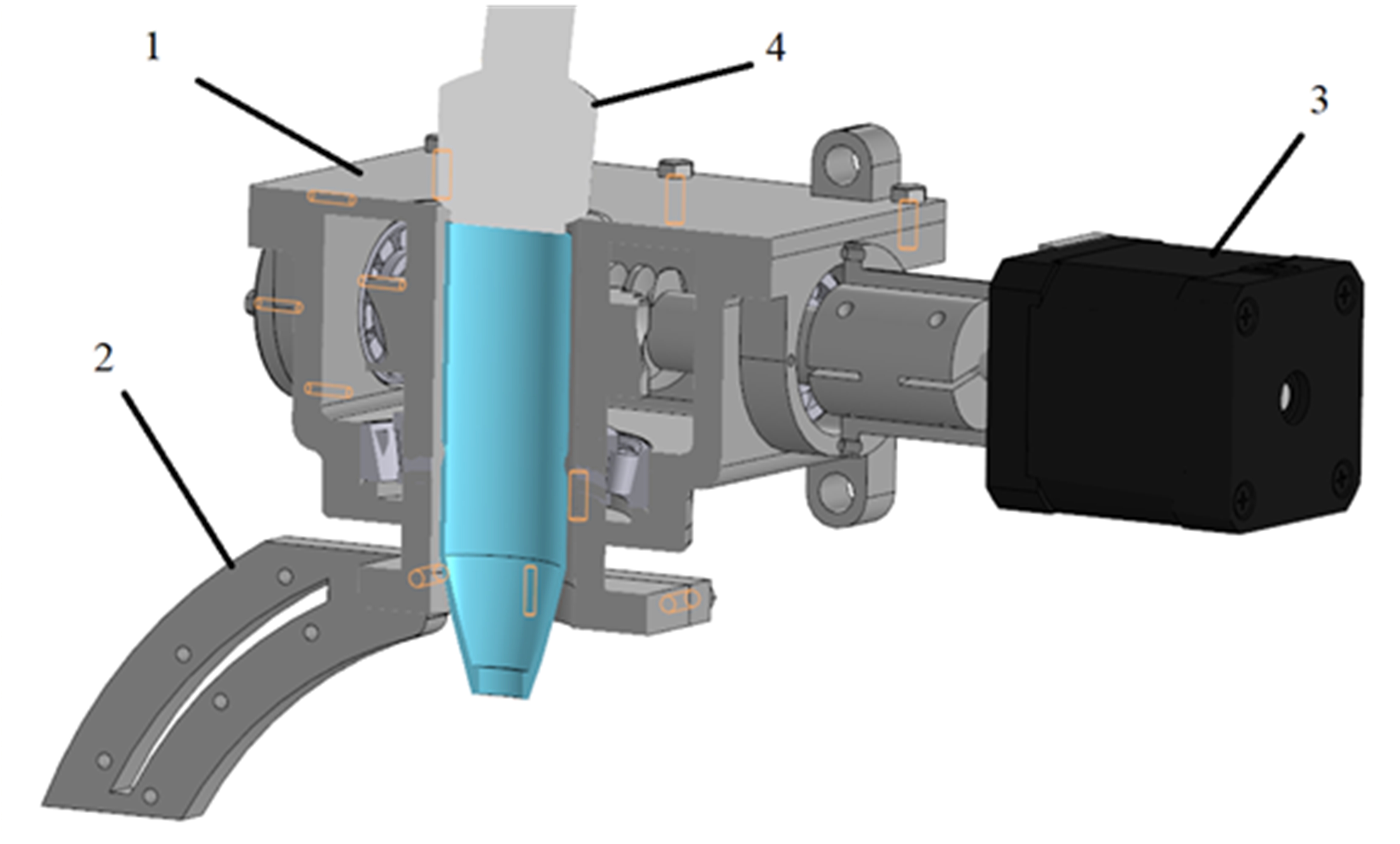
Рисунок 3 - Поворотный механизм:
1 - червячный редуктор; 2 - пластина регулировки наклона сопла с дополнительной проволокой; 3 - шаговый двигатель; 4 - горелка
3. Обсуждение
Таким образом, предложенные технические решения, кроме расширения технологических возможностей 3D печати за счет дополнительных поворотных устройств (появление 4-й координаты), способствуют также повышению плотности наплавленного материала, предполагают повышение уровня прочностных свойств. В качестве подтверждения работоспособности многофункционального оборудования и возможностей реализации на нем разных технологий формообразования можно привести пример изготовления подшипниковой опоры из проволочного материала АМг6 ГОСТ 4784-97. На основе наплавочного модуля и метода WAAM получена заготовка изделия (рисунок 4, а) на следующих технологических режимах 3D печати: ток в диапазоне 120-160 А, скорость подачи проволоки 0,8 м/мин. На базе этой же многофункциональной установки использован инструментальный модуль для механической обработки заготовки резанием (изображение детали после обработки на рисунке 4, б). Режимы резания для чернового фрезерования: глубина резания за проход, t = 0,5 мм, рабочая (минутная) подача, Sm = 700 мм/мин, скорость резания, υ = 471 м/мин, частота вращения шпинделя, n = 15000 об/мин. Режимы чистового фрезерования: глубина резания за проход, t = 0,1 мм, рабочая подача, Sm = 400 мм/мин, скорость резания, υ = 565,2 м/мин, частота вращения шпинделя, n = 18000 об/мин.
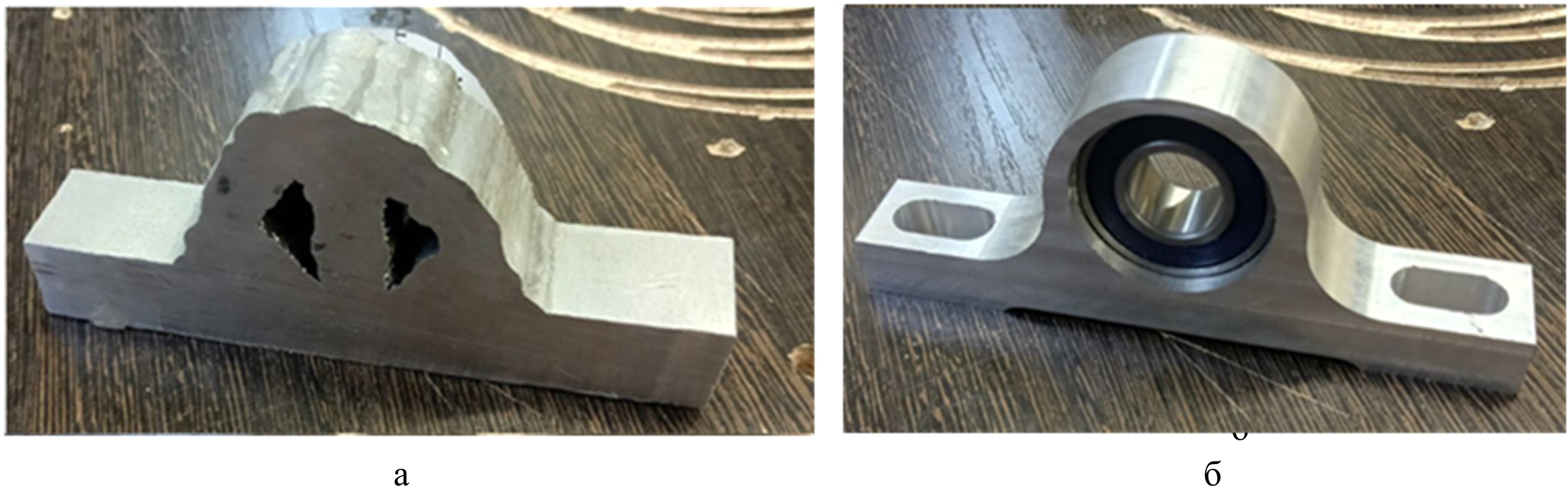
Рисунок 4 - Подшипниковая опора:
а - заготовка; б - деталь
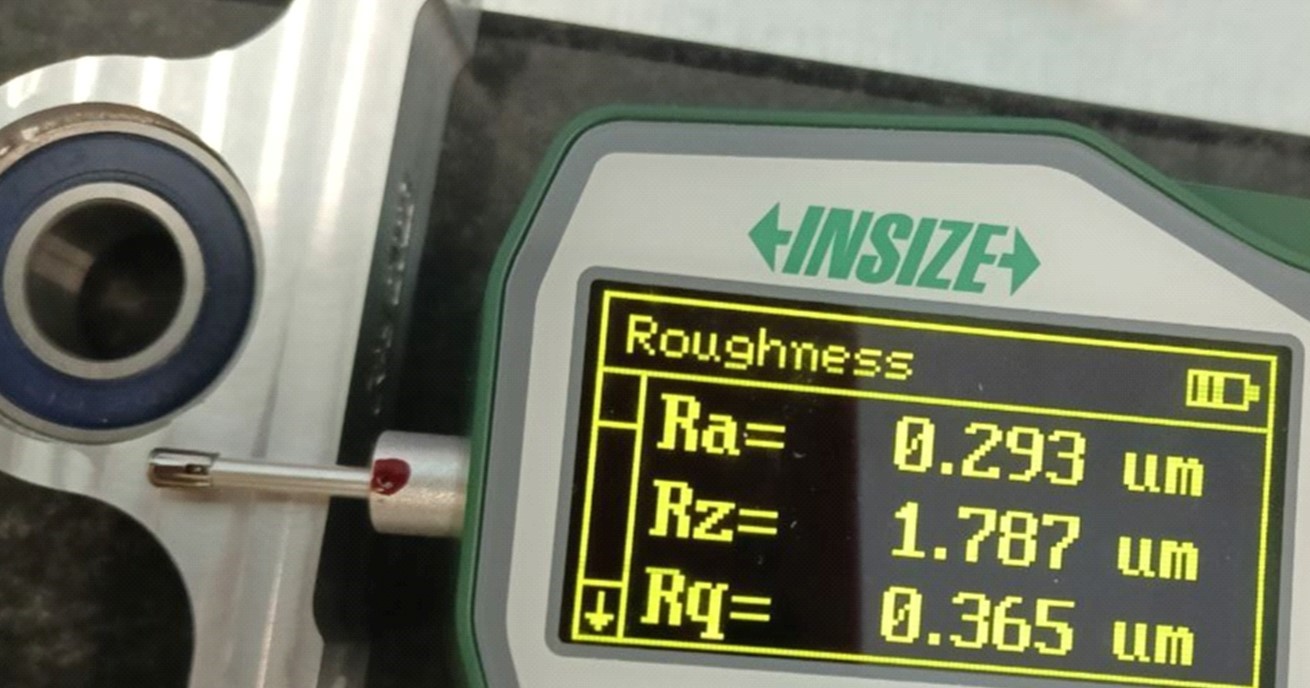
Рисунок 5 - Результаты измерения шероховатости поверхностей подшипниковой опоры: показания прибора
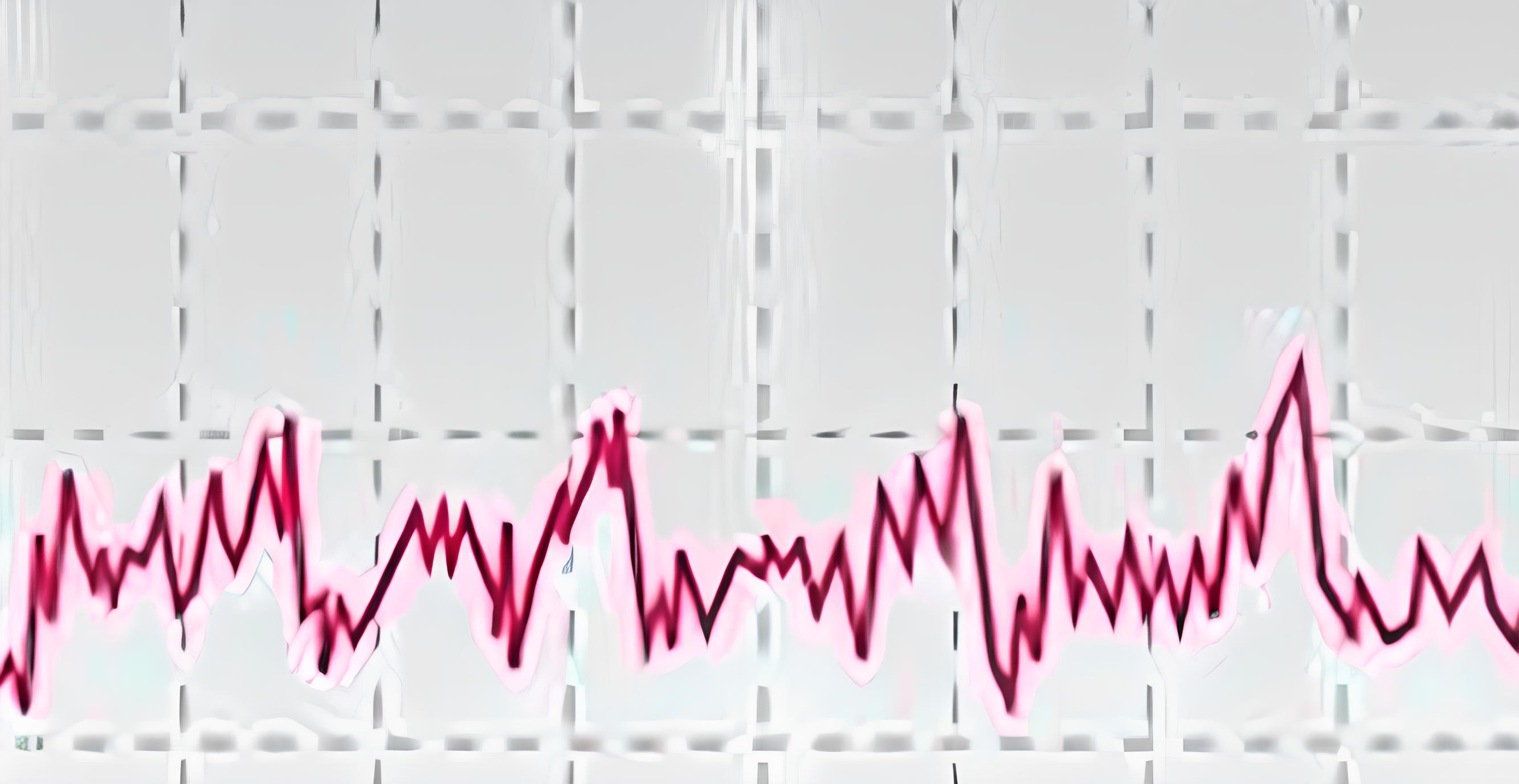
Рисунок 6 - Результаты измерения шероховатости поверхностей подшипниковой опоры: профилограмма обработанной поверхности
4. Заключение
Предложенные конструкторско-технологические решения, кроме расширения технологических возможностей разработанного многофункционального станка с ЧПУ за счет дополнительных инструментальных модулей, обеспечивает также и требуемый уровень качества поверхностей.